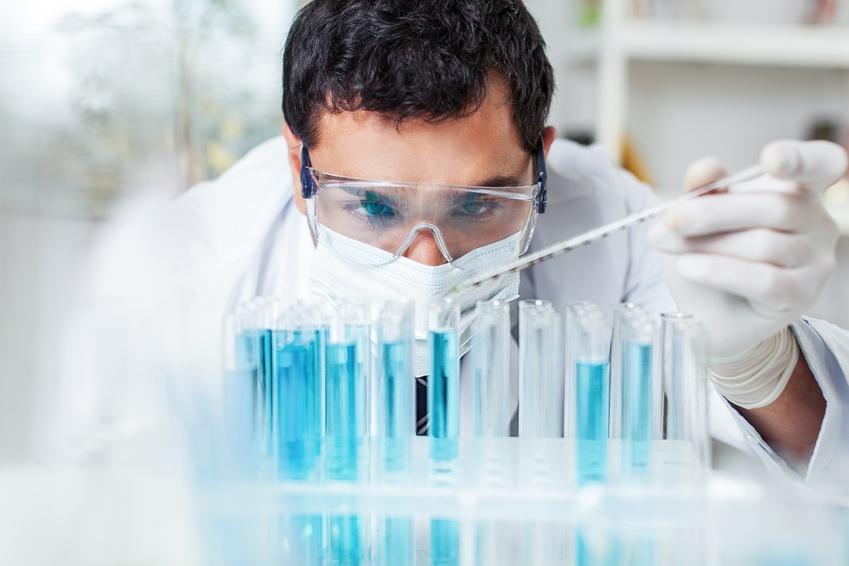
Chemical substances go through a long process before commercial use, and it's essential that all steps are followed in order to meet GMP standards. From checking for chemical purity, handling substances, and maintaining a cleanroom, chemical handlers, such as pharmacies, should oblige to all set standards.
How Do Chemical Manufacturers Assess Purity?
Assessing chemical purity is a vital process in assuring efficiency and quality of product. Chemicals can be analyzed in a few ways, with some being more effective than others. Visual comparisons between test substances and certified pure substances are a simple method to assess purity, but manufacturers and certified labeling companies may test a substance by using boiling temperatures, color reagents, or light-based analysis.
Light-based analysis, such as UV chromatography, is the most effective way to properly assess a substance and detect any impurities present. This method uses different lights and measures their absorption by the substance being tested. Ultimately, light-based analysis identifies the analytes of a given substance.
Once a chemical is properly assessed, trusted manufacturers and sellers will provide proof of analysis. This certificate indicates that a substance was tested for chemical purity, and that it has met its chemical standards.
The Importance of a Clean Workplace
Settings that deal with chemicals and pharmacology must then meet clean room standards. These regulations are met by properly maintaining chemicals and providing a clean workplace. Without clean room standards, disaster can emerge. In 2012, there was a meningitis outbreak in the US, and unfortunately, it was directly traced to a pharmacy in the Northeast. Evidence showed that certain procedures weren't followed and that GMP, Good Manufacturing Practices, were overlooked.
This occurrence is one that can be avoided by following the regulations that are set in place. Clean rooms serve a purpose in disallowing pollutants to infect the work area. Pollutants can lead to contaminated substances and, in turn, create an outbreak such as the one previously discussed.
Clean rooms are mainly kept by using air filters such as fume hoods. Air filters make certain that harmful contaminants are cleansed and unable to damage any products present. From then, a clean room is maintained by having workers wear suitable clothing. Clothing will depend on the clean room's classification, but it's important to follow the provided dress code in order to promote proper success in the workplace.
The Overall Importance of Chemical Testing and Workplace Precautions
Dealing with chemicals may be a long process, but it is one that can promote betterment of the workplace and provide safety for workers and the general public. Before distributing substances, it's important to get the most accurate reading of a chemical, and a certification of purity is assuring proof of analysis. From then, making certain that chemicals are stored in a proper environment that follows clean room standards is key to a balanced system.