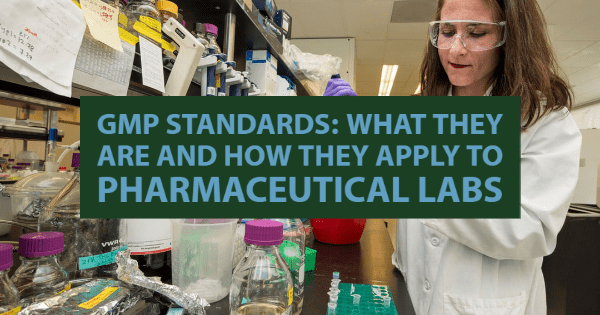
Perhaps there is no location that should be more carefully kept up and maintained than a pharmaceutical laboratory. Pharmaceutical labs are obviously responsible for creating and maintaining drugs and medications that will eventually be distributed to the general public.
In the past, it was difficult to maintain these labs at the correct standards, in part due to the fact that technology did not allow for it, and in part because standards were lacking at the time. This has led to multiple disastrous incidents. Bacteria and infections have been spread through drugs sourced at laboratories that were not properly maintained. Drugs had the potential to be tampered with as well.
However, as time has gone on, it's become easier for laboratories to be maintained as they should be. For example, clean room humidity levels can now be properly managed as close as plus or minus 1%, thanks to modern electronic sensing devices. With that being said, just because these technologies are available doesn't mean that they're used as they should be. This why GMP standards exist.
What Are GMP Standards?
GMP stands for Good Manufacturing Practice, and GMP standards essentially lay out the requirements through which goods should be manufactured. They ensure that goods are made in clean, safe, up to date environments, which ultimately results in safer, higher quality products that consumers can trust. GMP standards specifically apply to goods that are consistently produced in a controlled environment. Obviously, these standards wouldn't necessarily apply to custom-made goods, or goods made in a limited quantity. But they're effective when applied to laboratory environments due to the scale that they're created at. GMP standards can extend to GMP quality control and GMP storage conditions as well. In an ideal setting, they should really apply to the entire manufacturing process, from beginning to end. These types of standards are widely accepted as the best possible way to maintain quality levels. They'll vary somewhat from industry to industry, but on a large scale they are meant to keep production consistent and safe.
How Can Employees Be Trained In GMP Standards?
GMP standards are difficult to upkeep if employees are not aware of what they require. Therefore, it is up to laboratory administrators to ensure that their employees are trained in GMP compliance. This is often done through specific courses, and employees can become GMP certified. In some cases, employees can become certified through physical in-person training. However, this is often at least supplemented through online courses and webinars. While it may take some time for employees to become certified in GMP standards, this is about GMP quality assurance at the end of the day.
What Happens If GMP Standards Are Not Followed?
There are a number of risks that come with ignoring GMP standard, or failing to train employees in accordance to GMP compliance. A laboratory can certainly run the risk of being shut down if it fails to manufacture products in accordance to GMP standards. On a human level, the greatest risk is that people become sick through poorly maintained products. One relatively recent incident involved a 2012 outbreak of fungal meningitis. Incidents like this occur not only because the employees are improperly trained, but because tools themselves are not maintained. When an older or damaged production machine is used, products can be more easily contaminated.
GMP standards may at times seem to be somewhat excessive to some laboratory administrators, and certainly following them can require more time and investment than what may have been initially expected. However, these standards are meant to ensure that the safety and health of employees and the general public, and therefore they cannot be dismissed. In order to maintain practices in general, laboratories must follow GMP standards.