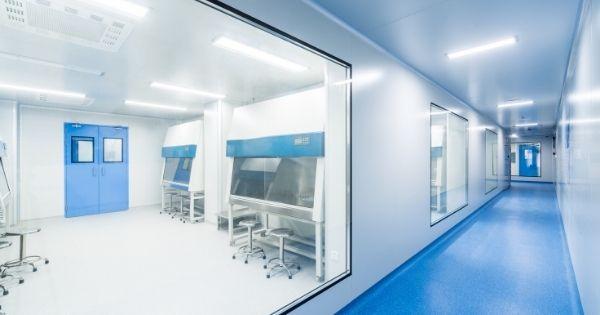
The high demand for cleanrooms across worldwide industries culminates a pressing need for avant-garde growth, reconfiguration, and pioneering innovations. Most unambiguously, the pharmaceutical manufacturing industry has a compelling demand for the enhancement of cleanroom technology. At their core, cleanrooms are ideal means for good manufacturing practices that prevent contamination during high-standard research and production procedures.
The controlled environment of a cleanroom is free of typical pollutants or impurities such as dust, chemical vapors, water vapors, minuscule microbes, and assorted airborne particles. The monumental augmentation is the ability to control the temperature, the direction and rate of internal airflow, and the pressurization within the room. Without the streamlined parameters and application of a cleanroom, many of today’s life-saving technologies would not be generated and advanced rapidly.
Companies or organizations that utilize sophisticated cleanroom technologies can better ensure that their products not only reach routine standards but go above and beyond in safety and superiority. While this mode of operation produces high-tech products or tech, cleanrooms still require fresh ideas and opportunities to improve the services they offer. Examine closer now a list of recent innovations in cleanroom technology that are changing the global market.
The Design of a Cleanroom
To reiterate, cleanrooms are remarkably designed with specific controls in respect to external and internal sources of contamination. Within the industry, there is a number of general classifications that differentiate the cleanliness of a room according to the size and count of particles in the process. By measuring the parts-per-cubic-meter, a cleanroom class designates the concentration of airborne particles. Ranging from ISO Class 1 to ISO Class 9, these numbers adhere to government regulations, or international standards, for heightened sanitation compliance worldwide.
Cleanroom infrastructures were originally built with one design—known as stick-built, built with individual construction parts onsite. However, there are other evolving design types that address common concerns over regulatory control and the efficiencies of cleanroom operation. These recent innovations in cleanroom technology are modern conceptions changing the cleanroom market as many industries once knew it.
Modular Construction Principles
Soft-walled modular construction materials are changing the industry for the better by optimizing the key factors necessary for ideal performance and final-result success. The trend of this alternative retrofit emerged as a design allowing the expansion of a cleanroom’s original layout. To the benefit of a facility, the major components making up the room are constructed offsite for ease of assembly on-site. The advantage of this type of cleanroom construction ensures ample opportunity for space and growth without the need to rebuild again from the ground up.
As an innovative designation of design, modularity allows for enhanced technological usage and flexible re-usage of space. Modular-designed cleanrooms are increasingly relevant these days due to the urgent need for rapid manufacturing responses and risk management. If any internal processes or external environmental factors are altered, the design can nevertheless adapt to these changes to remain efficiently cognizant of current needs.
Matter-of-fact, since modular cleanrooms have the ability to be changed or altered after a product’s lifecycle, they use fewer materials, reduce waste, and make the possibility of an energy-efficient cleanroom realistic. Instead of an overbuilt facility, modular cleanrooms are achieving a less energy-intensive and more resourceful controlled environment for the future.
Energy Efficiency: Greener Cleanrooms
Sustainability is a growing worldwide thought process that each industry must address for the benefit of future generations. Within the last decade, an assortment of cleanroom construction materials have been revamped, and a variety of sustainable practices have been implemented for the benefit of the environment. Cleanrooms traditionally utilize a collective sum of energy to maintain ideal controlled conditions, meaning creating greener cleanrooms is a top priority as of late.
Invariably, each cleanroom makes use of water, which calls for water conservation practices or technology. Ergo, manufacturing organizations can reduce water usage through energy-efficient, low-flow sinks. The usage of such energy-efficient equipment or LED lighting greatly supports sustainability efforts. Instead of the need for separate systems that use up further energy, organizations can utilize their own HVAC or ventilation systems.
With these strides toward green initiatives, the use of eco-friendly materials, and current sustainably-minded technologies, manufacturing companies can preserve resources while innovatively producing products. By implementing mindful considerations, further good can be put into the world—besides high-quality pharmaceuticals and life-saving research.
Cleanroom Robots and Isolator Technology
A wide range of valuable tools is available to support a heightened, continual level of cleanliness compact within cleanroom settings. Other technological tools are setting innovative benchmarks to offer support to cleanroom teams in the industry. Due to recent innovations in robotics, various new lightweight and compact robot offerings are being brought to the market for production use.
These robotic machines offer advanced motion control and handling capabilities to maximize productivity and ensure continuous accuracy. Though it’s a growing field, robotics provides lower manufacturing risks and refined performance to control contamination.
Other cleanroom solutions are accessible via isolator systems. Isolator technologies create the ability to maintain further levels of sterilization during pharmaceutical research and production. With the set-up and use of this equipment, cleanroom teams and operators can achieve higher purification levels.
The advantageous isolation system acts as a complementary barrier between a gowned operator and the product being manufactured. For existing cleanrooms, isolator technologies serve a functional purpose to improve manufacturing quality and apply greater flexibility in applications.
Contamination Control: Good Manufacturing Practices
Recent innovations of specialized surface coatings have come about to enhance sanitation during manufacturing. To prevent contamination, manufacturing organizations utilize good manufacturing practices (GMP) to prevent contamination in the controlled environments of cleanrooms. By following the standard GMP cleaning and sanitation procedures, cleanroom workers can better provide consistent cleanroom operations to develop Active Pharmaceutical Ingredients (APIs). API manufacturers utilize cleanrooms to safely develop effective drug products that are largely sensitive to microbes or particulates found in the air.
For quality API pharmaceutical manufacturing, reach out to Moravek.We are a highly experienced and trusted manufacturing organization that offers contract services for custom GMP API pharmaceutical manufacturing. Pairing alongside our expertise, we work to support companies and organizations in clinical research and trials. Our laboratory settings contain adequate cleanrooms to utilize all the benefits these controllable tools offer for the manufacturing needs of our partners. Contact us with any questions concerning our company or services.
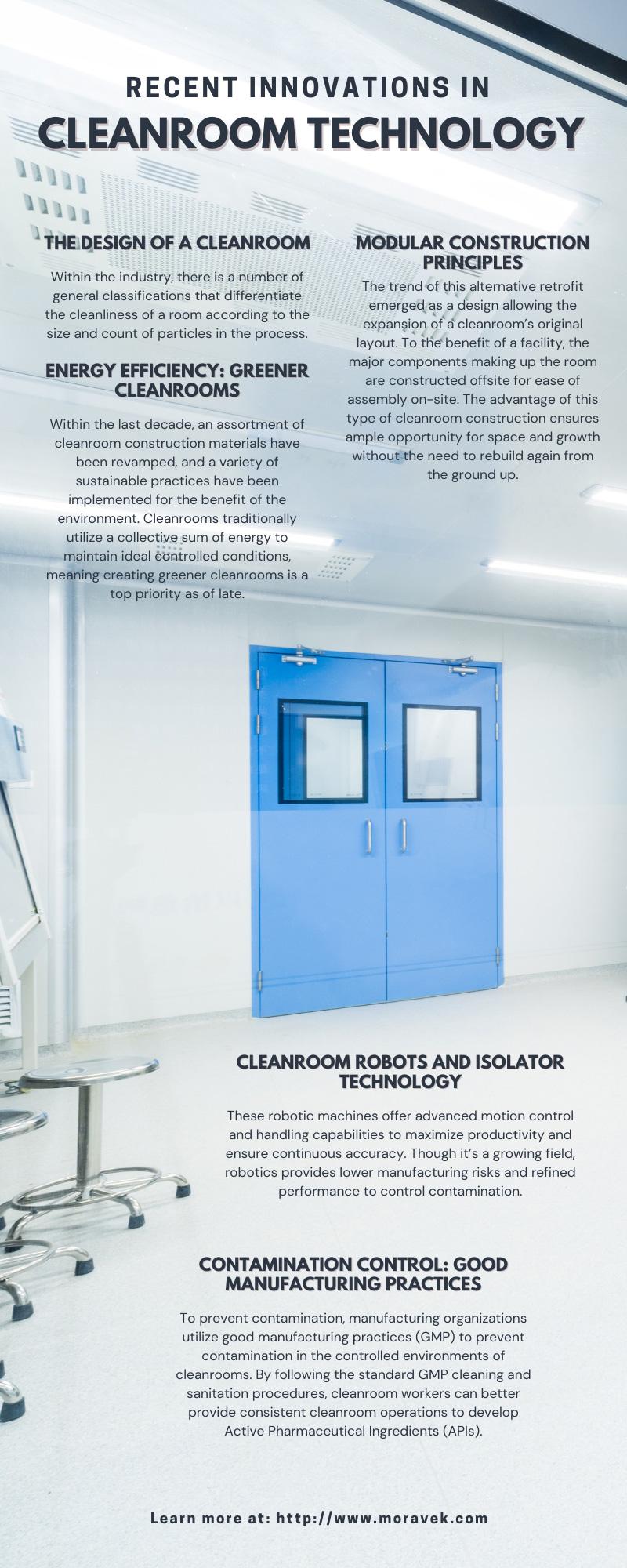