At Moravek, we use state-of-the-art instrumentation, equipment, and facilities to ensure that our GMP products meet our clients’ specifications and all essential regulatory requirements.
Instruments and Equipment in Support of GMP Manufacturing
All of the instruments and equipment used in support of GMP manufacturing are qualified by a certified Field Service Engineer for GMP use. We follow standard operating procedures (SOPs) for the use, cleaning, qualification, calibration, and record-keeping of our qualified instruments and equipment.
Moravek has a wide variety of qualified instrumentation available for use in the production and analysis of GMP APIs, including:
- Radiochemical purity
- Chemical Purity
- Assay
- Identity
- Molar activity (mCi/mmol)
- Identity
- Molar activity (mCi/mmol)
- Residual solvents
- Identity
- Elemental impurities
- Form (crystalline, semi-crystalline, or amorphous)
- Particle size distribution
- Identity
- Water content
- Weight
- Radio-concentration (mCi/mL)
- Total activity (mCi)
Moravek also has several data generation and storage solutions that are compliant with 21 CFR Part 11, such as:
- Agilent OpenLab Enterprise Content Management System
- Rees Scientific temperature, pressure, and humidity Environmental Monitoring System
- Mettler Toledo LabX Balance Software
State-of-the-Art Cleanrooms
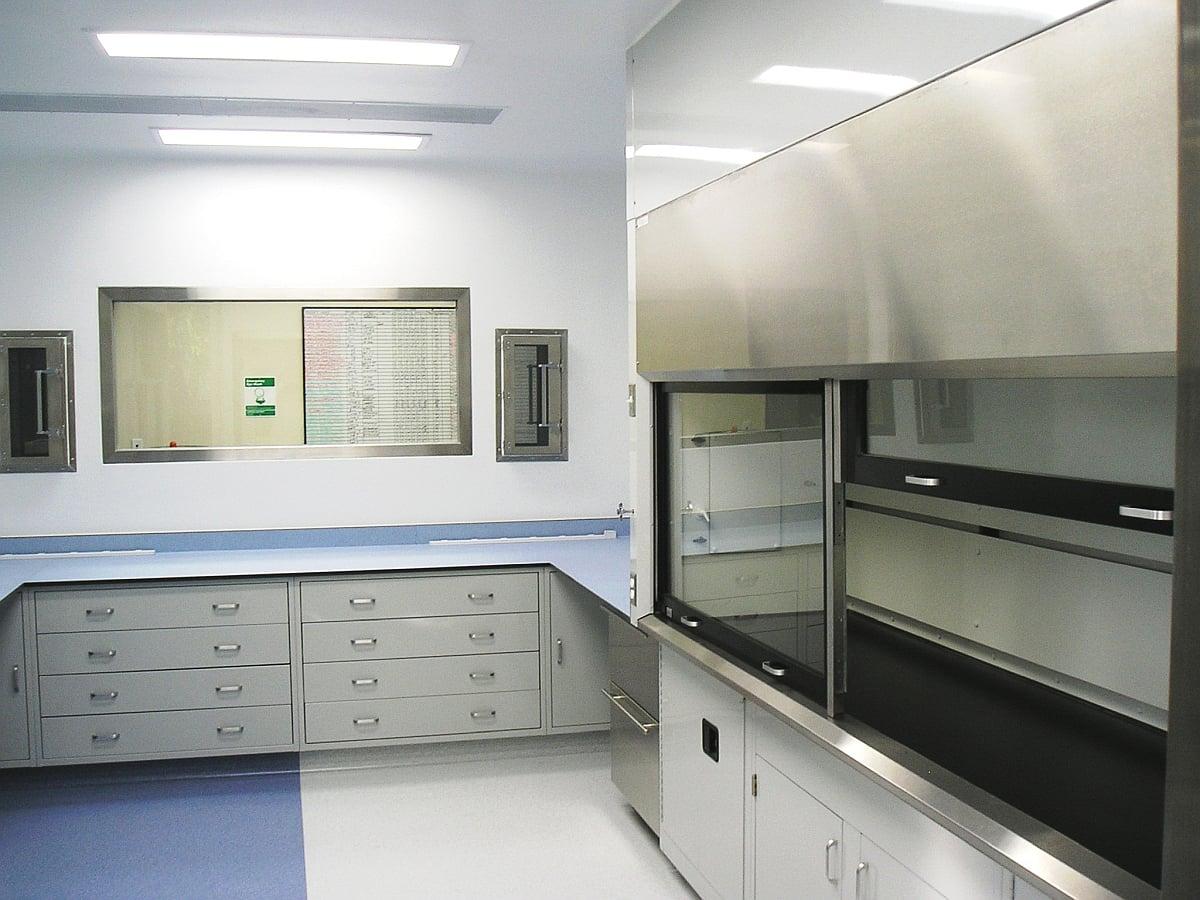
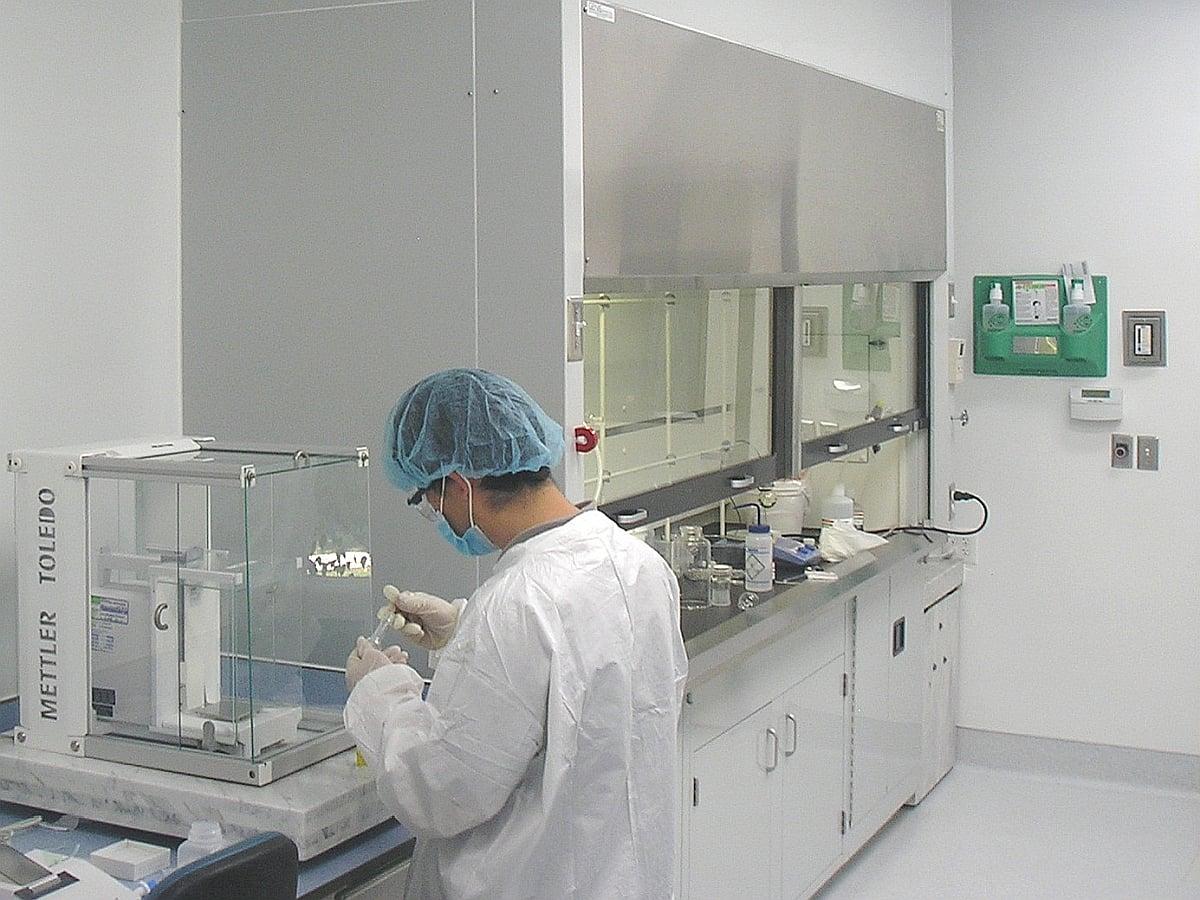
Moravek has four ISO Class 7 certified and qualified cleanrooms available for GMP production, each equipped with:
- Continuous recording of temperature, pressure, and humidity by Rees Scientific
- HEPA filtration and UV treatment of incoming air
- +4°C and -20°C in-process storage, with Rees Scientific temperature monitoring
- Qualified Mettler semi-microbalance
- Highly engineered walls, ceiling, flooring, and lighting to minimize dust and facilitate cleaning and maintenance
- Two-door pass-through chamber for analytical samples and final products
- Positively pressurized gowning area, with interconnected gowning area and cleanroom entry doors that cannot be opened at the same time
Prior to each GMP manufacturing campaign, the assigned cleanroom is cleaned and then verified by TOC according to standard operating procedures.
General Facilities
The entire facility operates with backup power via a 500-kW generator and automatic transfer switches. This Cummins, cloud-enabled, facility-wide backup power system eliminates any issues caused by disruption of power from the electric company, such as temperature excursions during storage of APIs. The generator has an 8 second response time and enough fuel for approximately 4 days of uninterrupted, full-scale operation.
The laboratory areas are controlled by a Brivo access control system that monitors and controls access to the facility and all of the restricted areas. Access is provided separately and on an as-needed basis to the restricted areas, including the non-GMP production areas, shipping and receiving, and each of the four GMP ISO Class 7 cleanrooms.