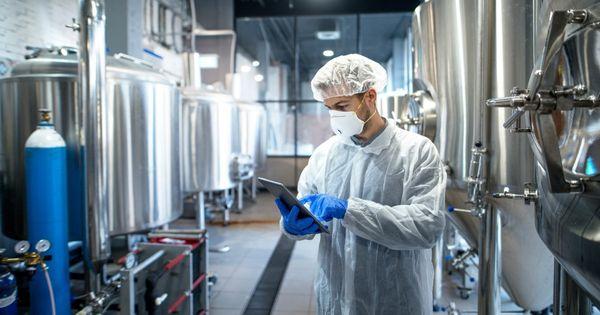
Every GMP-certified pharmaceutical manufacturer will encounter an audit for their GMP certification at some point. Things change, so these audits hold every business accountable. This is especially important in pharmaceuticals, as pharmaceutical quality affects consumers who take medication.
Sometimes, however, companies fail their GMP certification—find out the common reasons this happens below.
What is the GMP Certification?
GMP is an acronym for Good Manufacturing Practice. The FDA (Food and Drug Administration) put these standards into place to ensure products adhere to strict quality standards. GMP certifications aim to minimize the risks involved when producing products like medications.
GMP guidelines cover everything from employee hygiene to training equipment to manufacturing location to materials used in production. Companies must provide detailed documentation for every step in their manufacturing process to prove that they adhere to the guidelines. Consistency is key when it comes to GMP certifications.
Six P’s of GMP
Since GMP is about ensuring the consistent safety and quality of products, the focus is on the six P’s of GMP. The six P’s are proof, processes, products, people, paperwork (or procedures), and premises. The proof is the newest P added to the group. More and more consumers want evidence that the company is following GMP standards. After all, it can be the difference between an individual purchasing a product and leaving it on the shelf.
Reasons for Failed GMP Certifications
Passing GMP certification audits are essential for every company. These accreditations can uphold your company’s reputation, save your business money, and provide your company a competitive edge. Failing these audits will cause disruptions. Pay attention to these common reasons people fail their GMP certifications to avoid making the same mistakes:
- They provide inadequate cleaning validation, poor process validation, and poor equipment qualification. They fail to show improvement.
- Employees aren’t updated on their training or receive poor training.
- There are labeling errors on the product.
- There is insufficient environmental monitoring frequency and insufficient specified controls.
- The company is using unqualified suppliers or failing to maintain appropriate qualification records of the supplier.
- The business inadequately investigates and analyzes for root causes of issues, such as consumer complaints, product failures, and deviations.
Ensure you’re consistently following GMP guidelines, and your company shouldn’t have any issues passing and receiving the certification.
If you’re looking for a reputable, GMP-certified pharmaceutical manufacturer to do business with, look no further than Moravek. We take quality seriously, so you should choose us to provide API manufacturing services for your company. We look forward to hearing from you soon.